What is a smart actuator and how do HASEL actuators self-sense?
- eric5337
- Sep 9, 2021
- 3 min read
Updated: Feb 17, 2022
Connected, intelligent, and smart devices are all synonyms for similar desires: the ability to gather information about how a device is operating. Smart devices such as actuators are critical for the Internet of Things (IoT) and the Industrial Internet of Things (IIoT) applications. As businesses and applications look to optimize their operations, they want to make data-driven decisions by monitoring how various devices are operating and reacting accordingly. As a recent conversation with a Chief Information Officer highlighted, there is a large desire to “Connect and Collect” on any and all devices in their facility. The benefits of connected devices are endless, with readily available impacts on downtime, quality, safety, efficiency, and more.
A key need for increased connectivity is smart actuators, components that provide motion that can be highly controlled and monitored. HASEL actuators from Artimus Robotics are smart actuators. Using patented actuation technology, HASEL actuators are able to provide real-time information about their state and function thanks to the inherent self-sensing capabilities of HASEL actuators.
HASEL actuators are variable capacitors, consisting of opposing electrodes that partially cover a flexible polymer pouch that encloses a dielectric liquid. The HASEL actuator is activated by applying a voltage across these electrodes which drives a shape change in the pouch and is the fundamental mechanism for actuation. See this post and video for more details on how HASEL actuators work.
As actuation occurs (State 1 to State 2 in the image below), the capacitance of the actuator changes as does the distance in which the actuator has moved. Thus, a relationship between the capacitance and the distance the actuator has moved can be developed. The larger the capacitance, the larger the displacement of the actuator and vice versa.
Using patent-pending sensing techniques from Artimus Robotics, the capacitance of the HASEL actuators can be monitored in real-time, without an additional connection or sensing components. This technique uses AC impedance sensing, in which a low-amplitude, high-frequency AC signal is superimposed on to the high-amplitude, low-frequency driving signal that is driving the actuator. This methodology is often referred to as ‘Data-over-Power’ or ‘Power Line Communication’ in some communities. Proprietary analysis of this complex signal allows Artimus to gather feedback about the state of the actuator, enabling closed-loop control of the actuator.
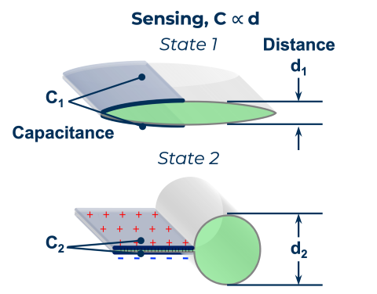
The self-sensing capabilities of HASEL actuators bring a variety of benefits to the customer of Artimus Robotics including the ability to operate in either force or displacement controlled methodologies. Additionally, the information gathered by the HASEL actuators during operation can provide information about the health or operating conditions of the actuators (example: failed vs operational) as well as information about the task and environment the actuator is operating in (examples: grip confirmation, actuation confirmation, system confirmation, and user or object behaviors and properties). Additionally, Artimus Robotics has developed a multi-channel sensing technique that can monitor the capacitance of multiple actuators simultaneously. Please contact Artimus Robotics at info@artimusrobotics.com with any questions regarding sensing.
About Artimus Robotics
Artimus Robotics designs and manufactures soft electric actuators. The technology was inspired by nature (muscles) and spun out of the University of Colorado. HASEL (Hydraulically Amplified Self-healing ELectrostatic) actuator technology operates when electrostatic forces are applied to a flexible polymer pouch and dielectric liquid to drive shape change in a soft structure. These principles can be applied to achieve a contracting motion, expanding motion, or other complex deformations. For more information, please visit Artimus Robotics or contact info@artimusrobotics.com.
Comments